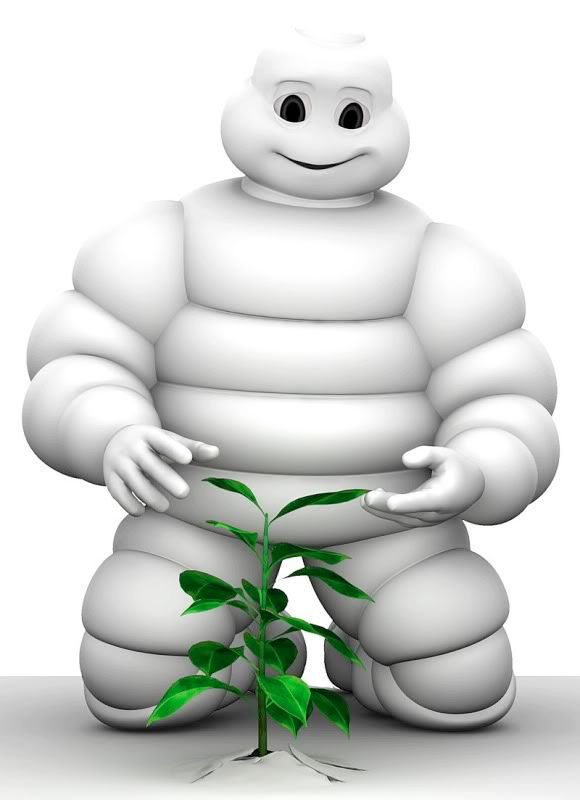
Los neumáticos viejos son difíciles de reciclar, y a menudo terminan acumulándose en vertederos específicos, pero investigadores del Centro de Investigación Mármara perteneciente al Consejo de Investigación Científica y Técnica de Turquía (Tübitak, por sus siglas en turco) han encontrado una nueva manera de tratarlos. Se les hace reaccionar con arena y se obtiene carburo de silicio, un material abrasivo que puede alcanzar los 10.000 € la tonelada.
El carburo de silicio, SiC, cuyo nombre comercial es carborundo o carborundum, se forma cuando los átomos de silicio y carbono se disponen en una red cristalina igual a la del diamante, lo que le confiere al compuesto algunas de sus propiedades más sobresalientes. Así, si en la escala de Mohs de dureza el diamante es el máximo, 10, el carborundo alcanza 9 o más. Tiene, por tanto, una amplia variedad de usos, desde abrasivos y herramientas de corte, a chalecos antibala y frenos cerámicos para coches deportivos. También se le emplea como semiconductor en aplicaciones de alto voltaje.
Habitualmente, el carburo de silicio se produce calentando arena (que es básicamente cuarzo, es decir, dióxido de silicio, SiO2) en un horno eléctrico con carbono obtenido a partir del petróleo o del carbón. La brillante idea del equipo de Tübitak ha sido obtener tanto el carbono como la energía necesarios de los neumáticos.
En primer lugar los neumáticos se gasifican, un proceso similar a quemarlos pero con una cantidad de oxígeno limitada. El resultado es la liberación de una mezcla de hidrógeno (H2) y monóxido de carbono (CO), llamada gas de síntesis, que deja un residuo de carbono elemental amorfo llamado negro de carbono. Los neumáticos también contienen azufre (S), que se añade como parte del proceso de vulcanización que convierte el caucho en un material resistente. La gasificación lo libera en su forma elemental, haciendo que sea fácil de recuperar. Quemar un neumático, por el contrario, produce dióxido de azufre (SO2), que es un contaminante tóxico.
El negro de carbono se mezcla entonces con arena y la mezcla se calienta a una temperatura entre 1400ºC y 2100ºC (dependiendo de las características de los reactivos) en un horno que usa como combustible gas de síntesis. El resultado es carburo de silicio de alta pureza. Bibendum se transforma en carborundum.
Tübitak es una de las nueve entidades que colaboran en un proyecto financiado por la Unión Europea, el proyecto TyGRe (Tyre Gasification Residues) para encontrar aplicación a las 325.000 toneladas de neumáticos que se envían a vertederos en Europa cada año.
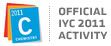
1 comentario:
un día me beberé un chupito de neumatico derretido..
Publicar un comentario